CLUM Series Feldspar Ultrafine Vertical Roller Mill
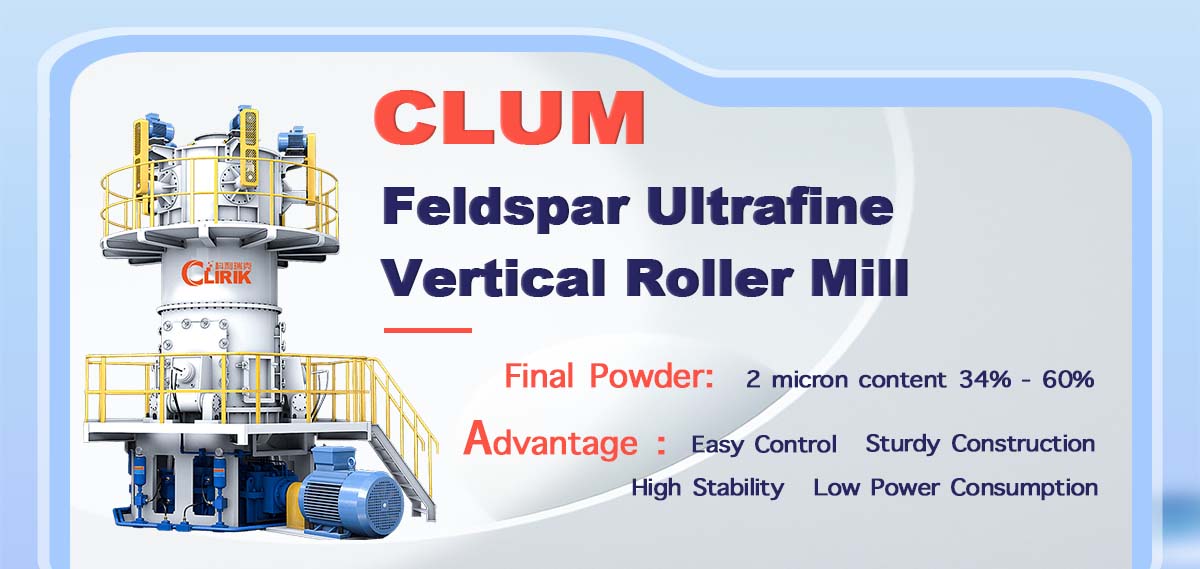
Brief Introduction
Introducing the CLUM Series Feldspar Ultrafine Vertical Roller Mill, a high-capacity mill designed for premium fine powder production. It offers a superior 2-micron content of 34%-60%, consumes 30% less power than ball mills, ensures reliability through multi-inspection systems, and features user-friendly PLC/DCS control.
Working Principle
Grinding Plate Rotation
The feldspar grinding plate is rotated by the main motor via the reduction gear. This is the initial step of the entire grinding process, providing the necessary power for subsequent material processing.
High-Pressure Air Intake
Meanwhile, high-pressure air enters the mill interior via the air inlet. This provides the necessary airflow for the grinding process, aiding in the transportation and grinding of materials.
Material Central Delivery
Materials then fall onto the center of the grinding plate in rotation by the screw conveyor feeder. This step ensures that materials are evenly distributed across the grinding plate, preparing for the subsequent grinding work.
Centrifugal Force Distribution
Due to the centrifugal force, the materials evenly move from the center of the grinding plate towards its fringe. This process helps in the uniform distribution of materials on the grinding plate, creating conditions for the next grinding step.
Direct Material Crushing
While passing across the track in the grinding plate, large blocks of materials are crushed and ground directly by the grinding roller. This is the physical crushing step in the grinding process, where large material blocks are initially broken down.
Material Bed Formation and Compaction
The fine particles form a material bed, owing to squeezing, where the inter-particle crushing takes place until ground to fine powder. This is a key step in the grinding process, where the interaction between particles achieves the final fine grinding effect.
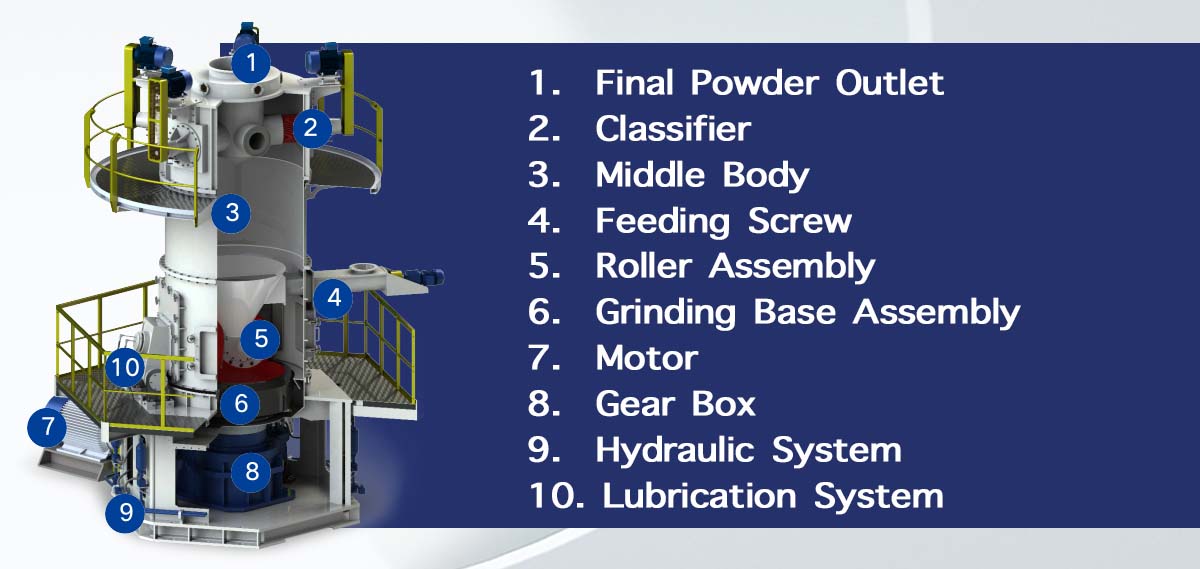
Application
CLUM series ultrafine vertical roller mill can be widely applied in the industries of chemicals, metallurgy, non-metallic ores etc. In particular, it is outstanding in processing white superfine non-metallic ore powders, providing superior quality fillers and additives for paper making, coating materials, plastics, rubber, PVC, printing ink etc. The CLUM mill can be extensively used to process superfine dry powder of non-mental materials such as calcite, marble, limestone, dolomite, talc, kaolin, wollastonite, gypsum, feldspar, pyrophyllite etc.
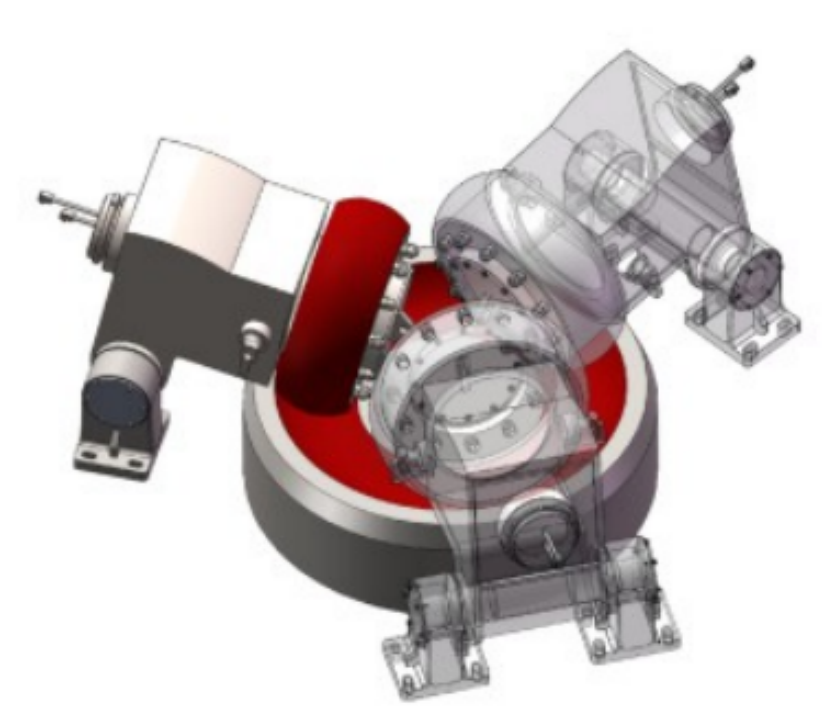
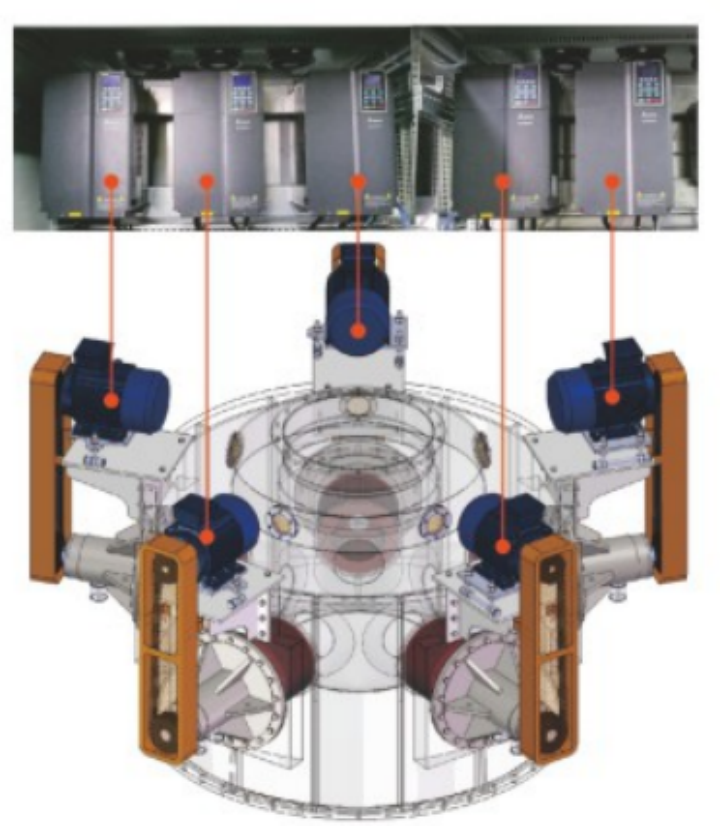
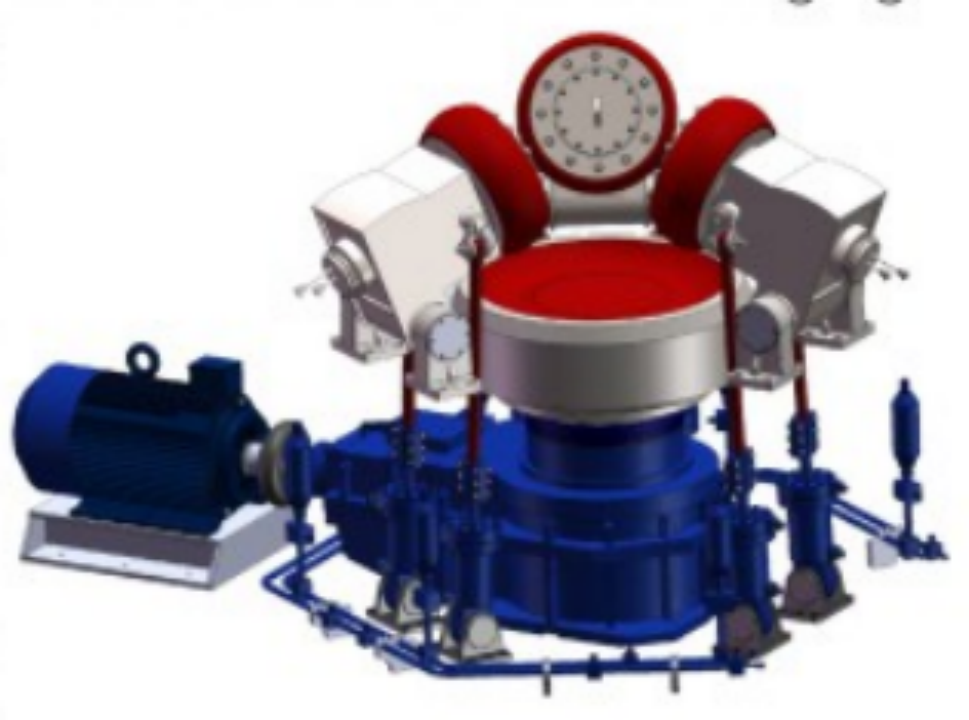
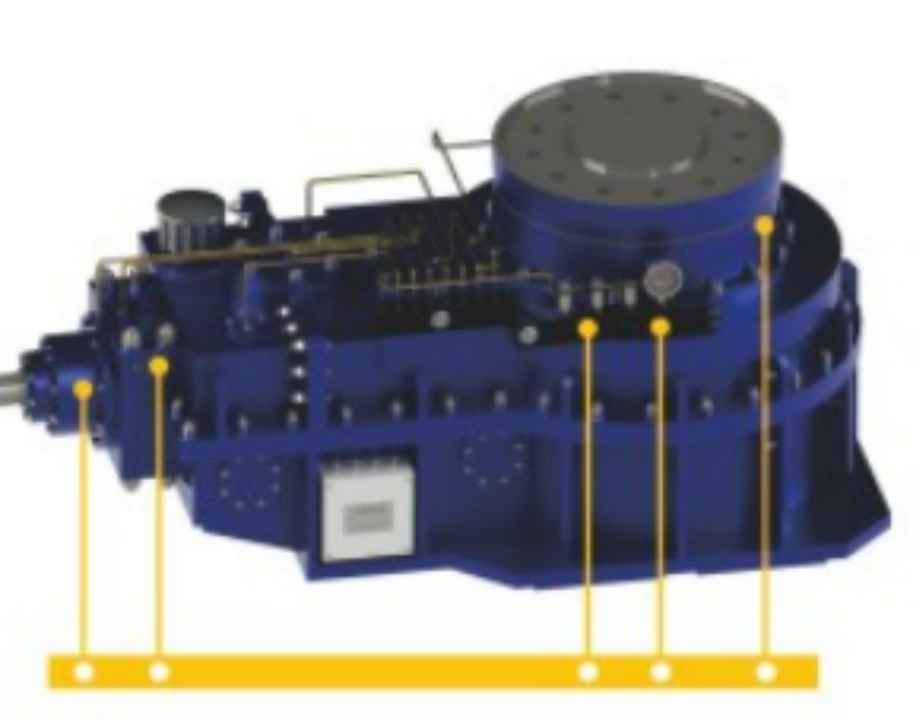
Advantage
Low Operation Cost
Grinding roller and plate liner liner are made of special alloy wear-resistant material, with long service life and low maintenance cost.
High Additional Value
The CLUM Mill has greatly increased the final powder added value and application areas due to the advantages of narrow particle size distribution, unit form particles shape and controllable 2 micron content.
Safe and Reliable
The pressure on the grinding roller controlled by the PLC/DSC system ensures precise control and high efficiency in the grinding process, without the need for manual operation, making the entire operation stable and safe.
Environmental Friendly
The whole equipment is sealed, and the finished product is directly sent to the finished product warehouse by the gas conveying equipment, without dust overflow, and the production environment is clean and environmental protection.
Technical Parameters
Model | CLUM1425 | CLUM1632 | CLUM1736 |
Plate Diameters (mm) | 1400 | 1600 | 1700 |
Number of rollers (pieces) | 3 | 3 | 3 |
Number of classifier (pieces) | 5 | 7 | 7 |
Powder of classifier (KW) | 5*15 | 7*15 | 7*(15-18.5) |
Main unit powder (KW) | 250 | 315 | 355 |
Blower powder (KW) | 200 | 250 | 315 |
Feed size (mm) | <10mm | <10mm | <10mm |
Moisture of feeding material | <3% | <3% | <3% |
Less than 2μ m=34% output (t/h) | 11-14 | 13-17 | 15-19 |
Less than 2μ m=46% output (t/h) | 7-8 | 9-10 | 11-12 |
Less than 2μ m=60% output (t/h) | 3-4 | / | / |
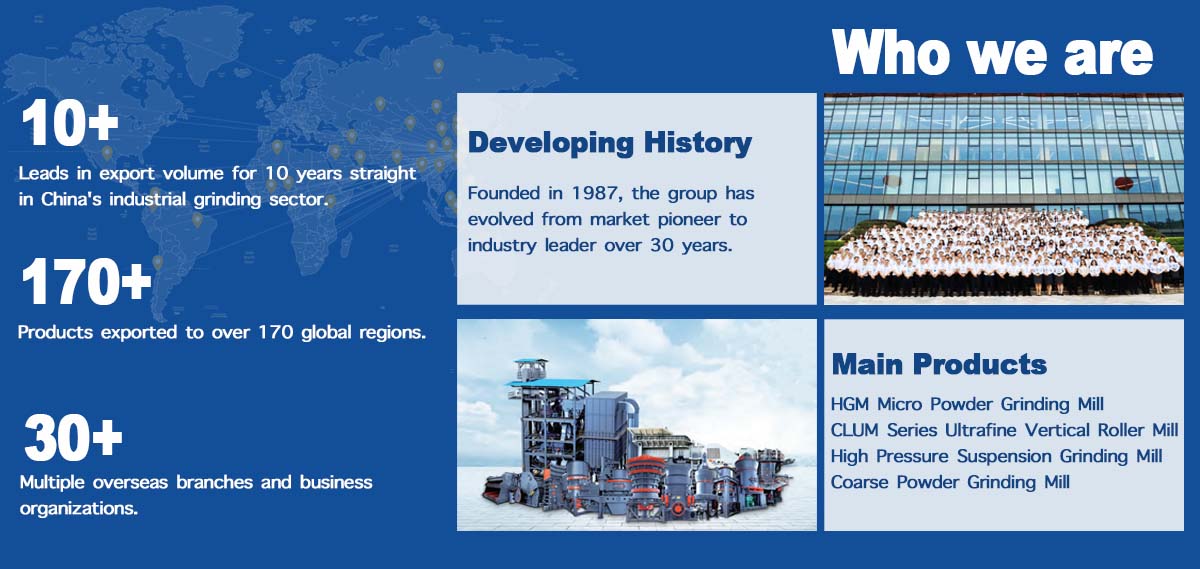