Feldspar High Pressure Suspension Grinding Mill
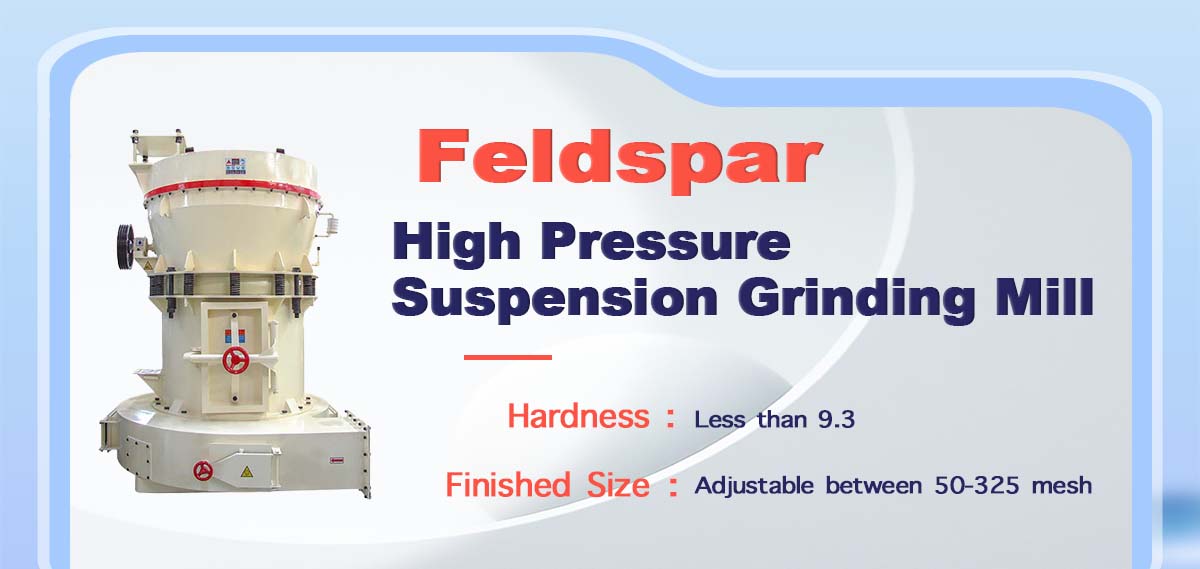
Brief Introduction
Feldspar High Pressure Suspension Grinding Mill is widely used in metallurgy, building materials, chemical industry, mining, highway construction and other industries. The Mohs hardness of the main processed materials is below 9.3, and the finished particles can be adjusted arbitrarily in the range of 50-325 mesh.
Application
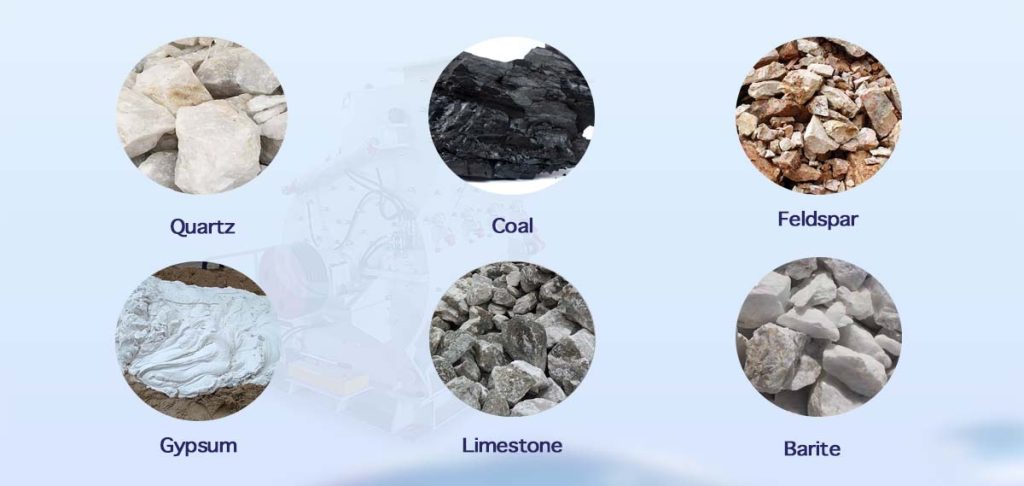
Work Principle
Crushing and Feeding
After being crushed by a hammer crusher, large materials are reduced to smaller sizes and are conveyed to a storage hopper via an elevator. Subsequently, they are evenly distributed to the upper distribution plate of the turn plate by a vibrating feeder and a sloping feeding pipe.
Mill Operation
The grinding mill operates with the main bearings and dials powered by an electric motor via a reducer. The grinding rollers move within the ring channels, propelled by plungers connected to the dials.
Centrifugal Force and Material Flow
Materials are propelled to the edge of the turn plate by centrifugal force and then fall into the grinding chambers.
Airflow Conveyance and Classification
A high-pressure air blower constantly inhales air. This air carries crushed materials to a classifier. Inside, a high-speed impeller sifts the airflow. Oversized particles drop and return to the mill for re-grinding. Correctly sized particles, now mixed with air, are funneled into a cyclone powder collector.
Powder Collection and Packaging
Most of the qualified powders will fall and exit from the discharging valve at the bottom; a small portion of the fine powders, carried by the airflow, moves to the dust cleaner. The materials from the above two processes are sent by a conveyor to be packaged into finished powders. In addition, the filtered clean air is emitted from the muffler at the end.
Advantage
High Efficiency, flexible adjustment
At the same time, the output of the machine is two copies of air mill and ball mill, and the finished particles can be adjusted arbitrarily in the range of 30-325.
Long lifecycle of spare parts
The ring and roller are forged by special material with high utilization, the lifetime can reach 2-5 years for grinding calcite carbonate.
High safety and reliability
As no rolling bearings or screws in grinding cavity, there are no problems caused by bolts shedding or rapid wear of bearings and seal components.
Environment-friendly
The application of pulse bag filter and muffler greatly alleviates dust pollution and noise.
Specification
Model | Roller Quantity (piece) | Roller Diameter (mm) | Roller Height (mm) | Ring Inner Diameter (mm) | Ring Height (mm) | Feeding Size (mm) | Finished Size (mm) | Motor Power (KW) | Capacity (t/h) | Overall Dimension (mm) |
YGM7815 | 3 | 260 | 150 | 780 | 150 | 15 | 0.613-0.033 | 18.5 | 1-3 | 4300*3500*5100 |
YGM8314 | 3 | 270 | 140 | 830 | 140 | 20 | 0.613-0.033 | 22 | 1.2-4.6 | 5300*4100*5200 |
YGM9517 | 4 | 310 | 170 | 950 | 170 | 25 | 0.613-0.033 | 37 | 2.1-5.6 | 7100*5900*7900 |
YGM4121 | 5 | 410 | 210 | 1280 | 210 | 30 | 0.613-0.033 | 75 | 2.8-10.5 | 9200*7250*9700 |
MTM1600 | 6 | 440 | 270 | 1600 | 270 | 35 | 0.613-0.033 | 132 | 5-15 | 12550*5700*8350 |
MTM1750 | 5 | 520 | 280 | 1750 | 280 | 40 | 0.613-0.033 | 180 | 7-25 | 11450*7610*9906 |
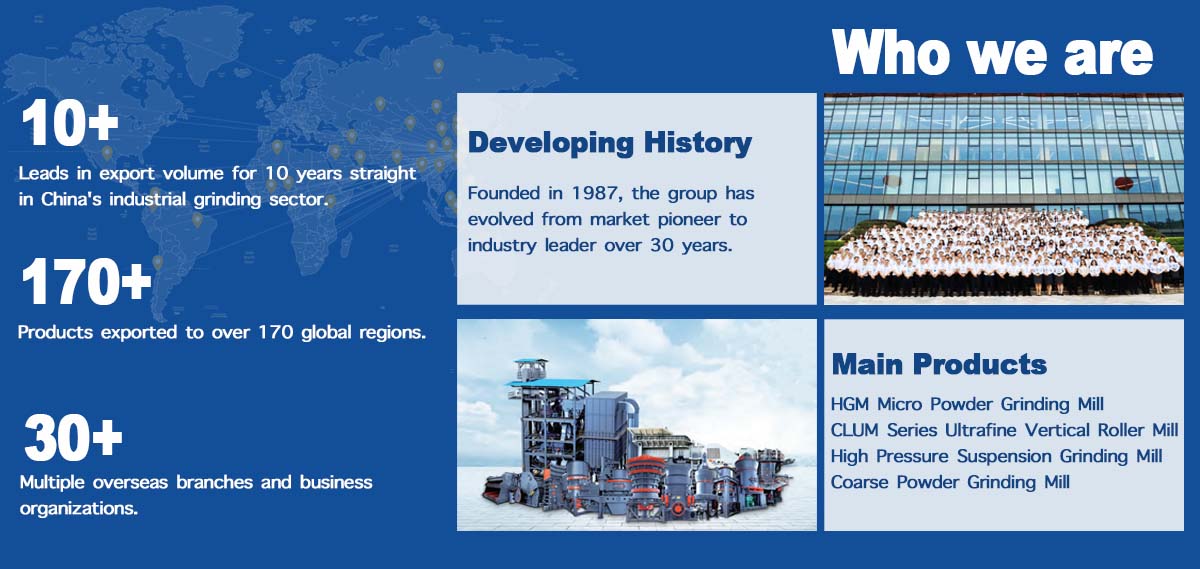